
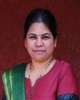
- Open Access
- Authors : Vani G. D , Pranay Sharma , Rajiv Satyakam
- Paper ID : IJERTV10IS080237
- Volume & Issue : Volume 10, Issue 08 (August 2021)
- Published (First Online): 09-09-2021
- ISSN (Online) : 2278-0181
- Publisher Name : IJERT
- License:
This work is licensed under a Creative Commons Attribution 4.0 International License
The Importance of Lubricant and Fluid Analysis in Predictive Maintenance
Rajiv Satyakam, Pranay, Vani G. D
NTPC Limited
Abstract::- Machine condition monitoring or predictive maintenance is the practice of assessing a machines condition by periodically gathering data on key machine-health indicators to determine when to schedule maintenance. One of the keys to keeping machinery operating at optimal performance involves monitoring and analyzing lubricant oils for characteristics such as contamination, chemical content and viscosity. Billions of dollars are spent annually replacing machinery components that have worn out due to the inability of the lubricants to perform the required task. Knowing how to interpret changing lubricant properties scan increase both the uptime and the life of your mission critical capital equipment. The existence or amount of debris and particles from wearing parts, erosion and contamination provide insights about the issues affecting performance and reliability. Lubricant, fuel and other key fluid analyses provide critical early warning information indicative of machine failure. Analyzing and trending the data means it can schedule maintenance before a critical failure. The result-higher equipment availability and productivity lower the maintenance costs.
Key words: Lubricant, Analysis, contamination
INTRODUCTION
Lubricants are the life blood of oil wetted machinery. As an important element of predictive maintenance technologies, in-service oil analysis can provide trace information about machine wear condition, lubricant contamination as well as lubricant condition (Fig.1) maintenance professionals can make maintenance decisions based on the oil analysis results. The immediate benefits of in-service oil analysis includes avoiding oil mix up, contamination control, condition-based maintenance and failure analysis.
Figure 1: Information provided by in-service oil analysis
Avoid Oil Mix Up
Oil mix up is one of the most common lubrication problems contributing to machinery failure, putting the right lubricating oil in the equipment is one of the most common lubrication problems contributing to machinery failure. Putting the right lubricating oil in the equipment is one of the simplest tasks to improve equipment reliability. Checking the viscosity, brand and grade of incoming new oil, and checking any contamination of alien fluids help reduce the chances of oil mix up and keeps the machine operating.
TURBINE OIL MIXING WITH CONTROL FLUID-ITS ENTRY ROUTE & IMPACTS
Mixing of turbine lubricating oil with FRF may take place through damaged governor below or o-ring part of speeder gear. It may also find its way into control fluid due to wrong oil top up by mistake or during crisis period. The control fluid gets emulsified due to non-compatibility between the two oil types. This drastically affects the appearance or clarity as well as modifies density, acidity, particle contamination level, kinematic viscosity & lubrication property in governing system depending on extent of mixing. Moreover, Lube oil mixing deteriorates fire resistant property of FRF in such mixture.
As turbine oil content in FRF exceeds 2.5% (by volume), transparency or clarity of FRF gets lost gradually as shown in Figure 2.
Figure 2. Clarity loss of FRF
Density of fresh FRF normally lies in the range: 1.05-1.15 gm/cc at room temperature but on increasing percentage of tube oil in FRF, density of emulsion gradually decreases as expected due to low density (0.86 gm/cc) of lube oil.
Reddish brown colored lube oil generally carries more oxidized oil components & acidic constituents (polar in nature) that interacts with polar part of FRF to contaminate it effectively (Figure 3)
Figure 3: Contaminated FRF by lube
Depending on quality of turbine lubricating oil and extent of its mixing, particle contamination level (ISO-4406/NAS- 1638 value) also changes by 1-2 units along with increase in acidity of control fluid.
Variation of kinematic viscosity of FRF emulsion is somewhat different depending on extent of mixing and homogeneity. Normal allowable kinematic viscosity range for governing system control fluid is 41.5-50.5 cst at 40oC. As the percentage of turbine oil increases in FRF, gradual change in viscosity follows a parabolic pattern (inverse U- shaped) that reaches a maximum value of 74 cst at (1:1) mixture and then again decreases.
Presence of turbine lubricating oil in governing system control fluid upto 2% by volume may not change a appearance of bulk fluid but mineral oil contains different polar additives & oxidized oil part that contaminates the FRF. Moreover, it becomes difficult for lube oil to sustain
/ function under high pressure & temperature, especially under super critical conditions. Non-compatibility effect of lube oil with FRF results increased viscosity and poor lubrication that may interfere with precise & rapid operation of control valve or to result spurious tripping.
RESULTS
Used Fire resistant fluid was having the following physic- chemical properties; moisture 550 ppm, acidity 0.012 mg KOH/gm oil, NAS value 7, whereas lube oil was having moisture 50 ppm, acidity 0.078 mg KOH/gm of oil & NAS value 9 after heating at 80 oC for 8 hours. Studies on oil mixing effect were also carried out under similar condition.
-
Kinematic Viscosity 45-46 cst at 40oC. In mixture as
% of turbine oil increases, viscosity of oil mixture gradually increased upto 74 cst at (50-50) and then again decreases and reaches close to viscosity of lube oil & FRF results increased emulsification that effects flow pattern or viscosity. In Tri-xylenyl phosphate ester, polar phosphate part remains innocent to non-polar paraffinic hydrocarbon chain. At(1:1)mixture of the two oils resulted maximum value of viscosity (74/75 cst).
Figure 4 : Kinematic viscosity of FRF
-
Flash point variation of FRF
FRF & lube oil samples were well-mixed in different proportions and flash point data obtained through Cleveland open cup method showed a gradual decrease in flash point with increase in concentration of lube oil in FRF (Figure 5).
Figure 5: Flash Point variation in FRF
Increasing or decreasing trend of acidity in emulsified FRF is dependent on relative amount of acidic constituents in FRF & lube oil.
So far health of control valve in turbine governing system is concerned mixing up of lube oil with control fluid (FRF) should be avoided in any case from safe operation point of view. It becomes difficult for mineral oil to withstand extreme pressure in governing system w.r.t oxidation / oil degradation and to offer good lubrication & fire resistant property especially when operating conditions are super critical or ultra supercritical. Beyond 2.5% by volume of lube oil in FRF makes the bulk fluid hazy due to non- compatibility and lowers flash point by around 2%. Also, abnormal viscosity characteristics of FRF emulsion may not offer correct lubrication to valve surfaces that may lead to cavitations, sluggish operation of control valves or may result spurious tripping of turbine. Turbine oil mixing incidents may be detected at the early stage as per described procedure in this paper to avoid major damage to turbine. Regarding separation methodology of turbine oil from FRF, may be consulted with NTPC-NETRA.
Contamination Control
Solid contamination (sand and dirt) accelerates the generation of abrasive wear. Liquid contamination such as moisture in oil accelerates machine corrosion. Fuel or coolant dilution in engine oil will decrease the viscosity therefore generating more adhesive wear (rubbing wear). It is critical to keep the lubricating oil clean and dry all the time. This requires that you set cleanliness limits and continue monitoring the contamination during the machine operation.
Oil Condition Based Maintenance
A well balanced oil analysis program can monitor machine wear condition, oil contamination and oil degradation at the same time. Key parameters are continuously tested and trending of those parameters is monitored. The frequency of testing/ monitoring of various parameters on routine basis will be as follows:
SL.NO.
Parameters
Frequency
1
Kinematic Viscosity( CST)
Once / week
2.
Neutralization No (mg KOH/gm of oil).
Once / week
3.
Water Content (ppm)
Once / week
4.
Mechanical Impurity (%)
Once / Week
Common In-service Oil Analysis Techniques
Table I shows typical oil analysis parameters and common analytical techniques to monitor machine wear, contamination and degradation.
Because different types of mechanical components tend to have various oil related issues, different oil analysis techniques might be applied. For example reciprocal engines tend to generate fine wear particles. Coolant leak, soot buildup and fuel dilution are common problems in lubricants. On the other hand, rotating machinery such as gear boxes tend to generate large wear particles. Acidity increase and moisture contamination are among common parameters monitoring lubricant condition to prevent corrosion. In almost in all cases, monitoring and maintaining lubricant viscosity within specification is critical to ensure mechanical components are well lubricated. Table 2 shows typical oil analysis parameters and how they relate to problems by equipment types.
CATAGORY
KEY ANALYSIS
ANALYTICAL TECHNIQUES
Machine wear
Fine wear metal elements
Rotating Disc Electrode (RDE) Spectroscopy, Inductive Coupling
Plasma (ICP) Spectroscopy
Large wear metal elements
Rotrode Filtration Spectroscopy (RFS), FP, XRF
Particle count and distributions
Particle count, Laser Net Fines
(LNF)
Wear particle shape analysis
LNF, Ferrography, Wear
Debris Analysis (WDA)
Contamination
Sand and Dirt
Particle count, Laser Net Fines
(LNF)
Water/Moisture
Infrared (IR), Karl Fischer Titration (KF)
Glycol/Coolant
Infrared Spectroscopy
Table 1: Key oil analysis parameters and corresponding analytical techniques.
Off-site Laboratories
Outsourcing oil analysis to an off-site oil laboratory is probably the oldest and most common approach in the industry. Every year millions of oil samples are analyzed by laboratories worldwide. A typical process flow involves a user collecting oil samples from equipment and shipping them to a lab, lab technicians performing requested oil analysis tests, and an analyst reviewing the data and providing
CATEGO RY
DIESEL ENGIN E
GEAR SYSTEMS
HYDRAULI C SYSTEMS
Elemental
Wear, contamin ants, additives Viscosity
–
contamin ation from soot, or fuel
Gear boxes generate all sorts of wear, but the levels can sometimes get confusing
Will often
validate or clarity particle count; added value for additives and contaminatio n
Particle Count
–
Quantitative
Ferrograp hy
Tracks the large iron- laden particles for Analytical Ferrography trigger
FTIR
Oxidatio n, nitration combusti on byproduc ts, glycol contamin ation
Oxidation, base stock integrity
Oxidation, base stock integrity
Viscosity
Commun ication from soot
Always useful and worthwhile
Always useful and worthwhile
TAN
Contamination or degradation
Contaminatio n/degradation
Water
Mostly to indentify
To validate the sample
Any detectable amount is probably abnormal or critical need particle count validity check
CATEGO RY
DIESEL ENGIN E
GEAR SYSTEMS
HYDRAULI C SYSTEMS
Elemental
Wear, contamin ants, additives Viscosity
–
contamin ation from soot, or fuel
Gear boxes generate all sorts of wear, but the levels can sometimes get confusing
Will often
validate or clarity particle count; added value for additives and contaminatio n
Particle Count
–
Quantitative
Ferrograp hy
Tracks the large iron- laden particles for Analytical Ferrography trigger
FTIR
Oxidatio n, nitration combusti on byproduc ts, glycol contamin ation
Oxidation, base stock integrity
Oxidation, base stock integrity
Viscosity
Commun ication from soot
Always useful and worthwhile
Always useful and worthwhile
TAN
Contamination or degradation
Contaminatio n/degradation
Water
Mostly to indentify
To validate the sample
Any detectable amount is probably abnormal or critical need particle count validity check
Table 2: Different oil analysis parameters by machine applications
Recommendations. The report is then sent to the management team for review and it needed, maintenance actions are performed. Taking into account the recommendation and maintenance schedule(Figure.6)
Figure 6: Off-site oil analysis flow chart
TABLE III: IS 1012:2002, ref: IS 1448
S.No
Characteristics
VG 32
VG 46
Recommended Range
a.
*Moisture Content mg/lw/w
<100
(Note 4)
<100
(Note 4)
b.
Kinematic Viscosity at 40 deg. C, centistokes (cSt or mm2/s)
28.8 35.2
41.4 50.6
c.
Viscosity index, min
100
98
d.
Acidity inorganic (mg KOH/gm of oil)
Nil
Nil
e.
Flash point (Cleveland open cup.)0 C min
190
200
f.
Emulsion characteristics, Max
40-40-0
(20)
40-40-0
(20)
g.
Total AcidNumber (TAN), mg KOH/g oil
0.3
0.3
h.
Foaming Characteristics max.
300/Ni l25/Nil 300/Ni l
300/Ni l25/Nil 300/Ni l
i.
Air release value, at 50deg. C. Maxin minutes.
5
6
j.
*Accelerated ageing test (RPVOT), Minutes (Min)
200
200
-
at 24 deg. C
-
at 93.5 deg. C
-
at 24 deg. C after testing at 93.5deg. C.
TO BE USED WITH THE TABLE NO. III
-
The recommended frequency of all above tests may be increased if problems with the plant or the lubricating oil are being experienced.
-
The requirement of IS 1012:2002 is that oil should be visually clear and free from water, suspended matter, dirt and sediment. Some darkening with age is to be expected which is not detrimental to the performance of the oil.
-
The moisture content of turbine lubricating oil varies widely with plant design and operational practices, although, it is desirable to keep the moisture content as low as practicable and below 100mg/l. If this is not achievable with some plant, excursions above 100 mg/l may be experienced.
-
Tribology Lab (TL)
A TOTAL Tribology Lab (ITL) contains a complete set of oil analysis instruments suitable for performing the most demanding in-service oil analysis task commonly performing the most demanding in-service oil analysis tasks commonly performed in a commercial laboratory
(Figure 6). It is designed small footprint (Suitable for on- site or in a trailer), no sample preparation (Suitable for reliability professionals), low consumable cost, low waste stream, and ease of use.
The core instrumentation of a TL includes a Rotating Disc Electrode (RDE) Optical Emission Spectrometer (OES), a direct imaging particle analyzer based on Laser Net Fines technology, a temperature controlled viscometer, and an infrared spectrometer and information management software.The RDE-OES (Spectroil Q100) provides an elemental breakdown of fine and dissolved wear metal particle concentration in parts per million (ppm). It uses 2ml of oil sample and only takes 30 seconds to analyze up to 32 elements at once and complies to ASTM D6595.
The Laser Net Fines (LNF) particle analyzer uses direct imaging technique with a high speed CCD camera to capture particles in oil .The infrared spectrometer (Fluid Scan) is based on diffraction grating optics instead of the FTIR technique. It complies with ASTM D7889 which provides a dedicated oil analysis spectrometer based on diffraction grating and more repeatable and reproducible oil chemistry information than the FTIR method. It also includes a large on-board oil library with accurate TAN, TBN and dissolved water information without the needs of titrators. Ferrography (ASTM D7684, ASTM D7690) can be added in the ITL configuration as well or advanced failure analysis. Instruments only standardization and a regular performance check is needed
MINI AV |
TAN |
MOISTURE ANALYSER |
FLASH POINT ANALYSIS |
RUST CHARACTERSTICS |
Water Separatability |
Figure 6: TL configuration
CONCLUSION
In summary, in-service oil analysis provides critical information about machine condition and oil condition. There are may different approaches to implement an oil analysis program, depending on the application and maintenance objectives. Modern technologies have enabled reliability professionals to use new tools for the highest level of efficiency and effective maintenance.
ACKNOWLEDGEMENT
Author is thankful to Shri.Shawattam, GM-NETRA for their continued interest on new areas of power plant chemistry & and thrust towards exploration of modern condition monitoring techniques for sustainable development at this competitive power sector environment.
Contributions of colleagues who have helped directly or indirectly in writing this article are also gratefully acknowledged.
REFERENCES
-
Ken Brown; Managing the health of Fire resistant Steam turbine Electro-hydraulic control oils, Machinery Lubrication, May-2001.
-
L. Cho and E.E.Kaus; Oxidative degradation of Phosphate esters, ASLE Transactions; Vol. 24, 119-124, 2008.
-
R.R Van de Voort, J. Sedman, R.A.Cocciardi; Condition monitoring of In-service lubricants: Ongoing developments & Future perspectives, Tribology Transaction; 49, 410-418 (2006).
-
Technical bulletin and MSDS of Fyrquel EHC/ECH-N from ICL America Inc., USA.
-
Technical bulletin and MSDS of Reolube 40XC from Kemture Corporation, USA.
-
S.M. Hsuet.al.; Oxidative degradation mechanisms of Lubricants, ASTM special technical publication, Philadelphia, 1983.
Rajiv Satyakam B.Tech(Mech), M.Tech has more than 30 years of work experience in field of CFD, Ash utilisation, Waste to Energy, Bio-mass & Bio-Fuel, Metallurgy Lab and AUSC, Design, Engineering, Operation and Maintenance of various NTPC thermal power projects etc. He is having various research publications in International & National journals and various papers presented in International and National conferences/seminars/workshops. |
|
Pranay M.Sc. (Chem.), M.Tech has 15 years of work experience in field of ash utilization, biomass & coal combustion, commissioning and operation of D.M. Plant, Coal and Combustion of thermal power plants. He is having various research publications in International & National journals and various papers presented in International and National conferences/seminars/workshops. |
|
Vani G.D M.Sc.Engg by Research has 10 years of work experience in the field of Oil Tribology, Air preheaters, bowl mills and Rotary parts of power plant machineries, Sophisticated Instrumental analysis and Conditioning assessment of Lubricating oil analysis. Presently working as Manager (NETRA) |